Rebuilding a Torpedo Freilauf hub
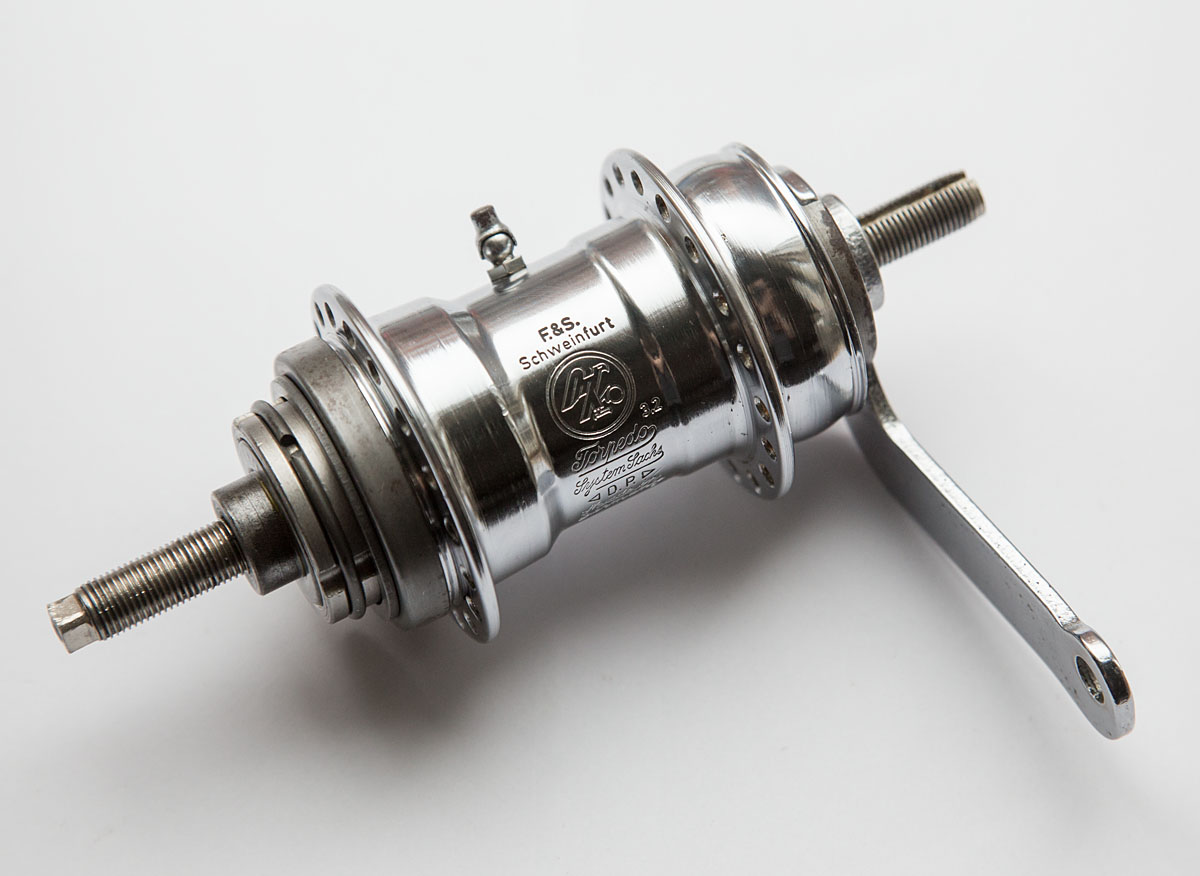
The old F&S / Sachs Torpedo coaster brake hubs are very robust and can provide decades of problem-free operation if properly lubricated and dirt and water is kept out of the internal mechanism. The original version from 1909 (also called model 09/10) remains mostly spare part compatible with later revisions. Let us overhaul this good looking example from 1965.
There is also a later revision of this hub with a grooved/rippled hub shell with the model number T1210. It is mechanically the same.
Notice the step in the diameter of the drive side of the hub. This distinguishes it from the otherwise similar-looking cone-drive Torpedo Komet and Jet hubs.
Notice the step in the diameter of the drive side of the hub. This distinguishes it from the otherwise similar-looking cone-drive Torpedo Komet and Jet hubs.
The freewheeling mechanism works by having ramps with carefully angled profiles lock five rollers against the inner hub shell bore when the driver is turned.
Here shown from the left side. The hub shell and driver rotates counter-clockwise when pedaling.
To the left, the driver is in the freewheeling (or braking) position. To the right, the rollers are locked against the hub shell bore.
Here shown from the left side. The hub shell and driver rotates counter-clockwise when pedaling.
To the left, the driver is in the freewheeling (or braking) position. To the right, the rollers are locked against the hub shell bore.
The original parts list and exploded-view drawing:
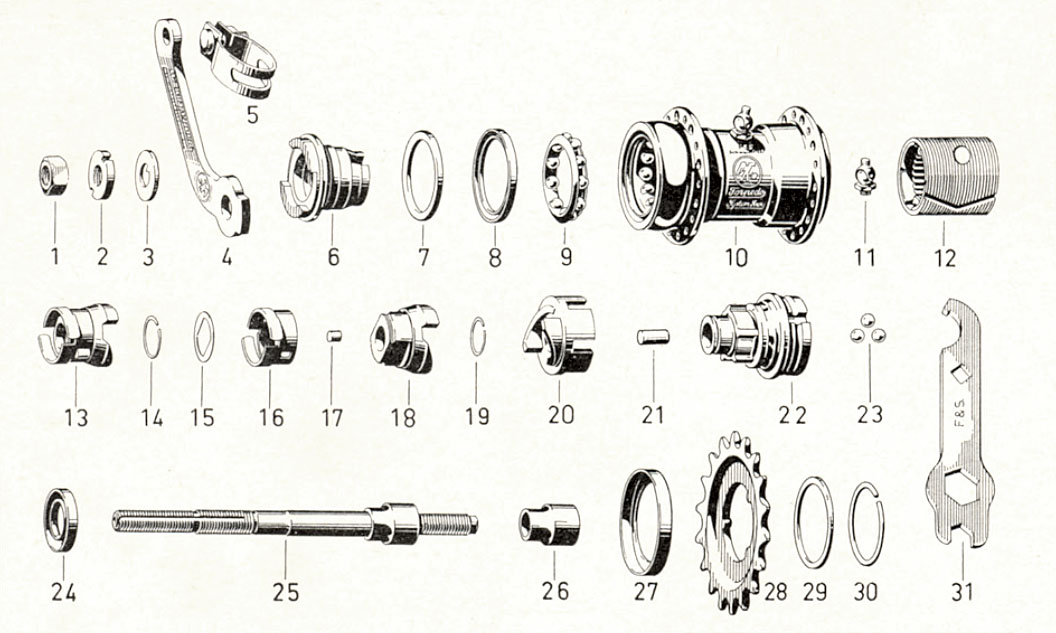
- Hex nut 9.5 mm 3/8" 26 TPI (2)
- Cap nut 9.5 mm 3/8" 26 TPI
- Lock washer
- Brake lever
- Brake arm fitting
- Lever cone
- Lever cone cover
- Press-in cap for hub shell
- Ball bearing (2)
- Hub shell
- Lubrication nipple
- Brake Cylinder
- Brake cone assembly
- Circlip
- Washer
- Friction spring sleeve
- Roll 4.5 mm (2)
- Brake cone
- Circlip
- Roller guide ring
- Driving roll 6.5, 6.6 or 6.7 mm (5)
- Driver
- Ball bearing ring or 10 loose 1/4"
- Dust cap for driver
- Axle with fixed cone
- Fixed cone
- Dust cap
- Sprocket, push-on type
- Washer
- Circlip
- Hook spanner
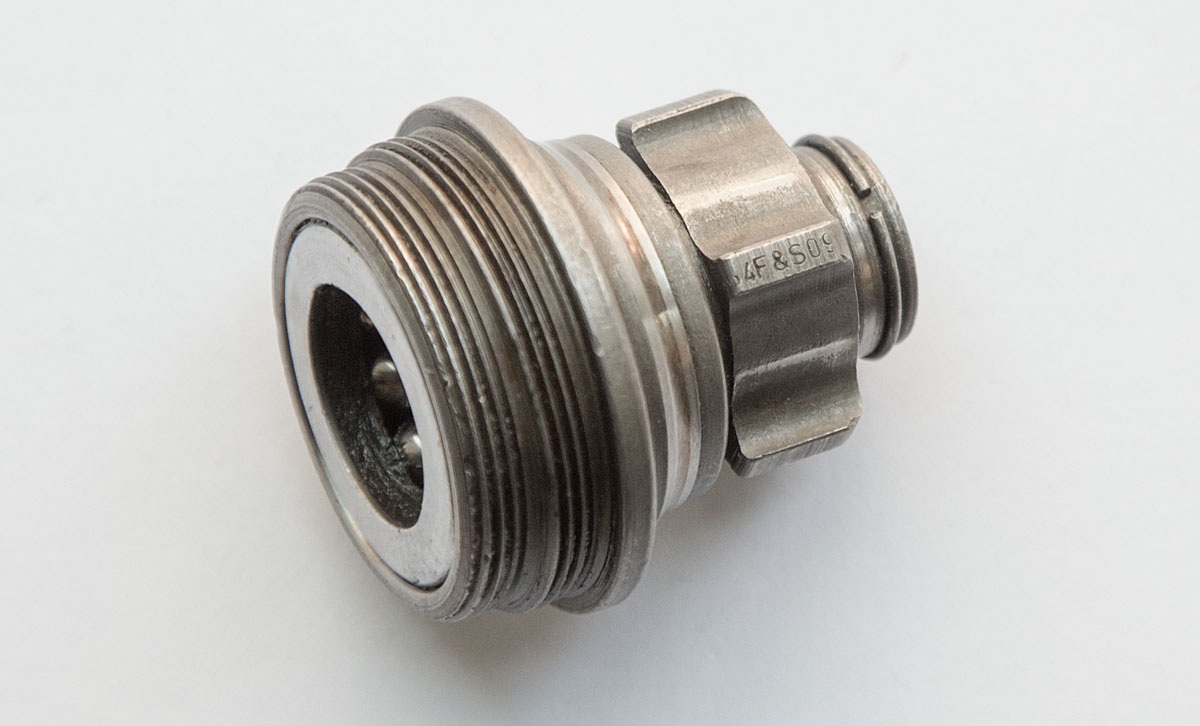
The inner, larger diameter thread for the sprocket is standard BSA/ISO 1.37" x 24TPI AKA FG 34.8mm also used for freewheels and fixed-gear cogs for track hubs. The smaller outer diameter for the lock ring is left-hand-threaded 1.29" x 24TPI AKA FG 32.8mm (as far as I can figure out). Be aware of the width of the threaded part of the sprockets, as new-production cogs for track hubs tend to be a bit wider, resulting in the lock ring engaging in fewer threads, which is not safe. This guide shows how to modify a wide-threaded sprocket to make it fit. Also, note that there is a special Italian lock ring threading size used on for example Miche track hubs that is slightly larger diameter (1.32" x 24TPI, around 33,5mm) that will NOT properly fit a Torpedo driver.
Replacing a threaded sprocket requires the driver to be removed from the hub, as the substantial torque often needed to loosen a stuck sprocket can damage the coaster brake components. The later snapring mounting system made changing sprockets much quicker and easier.
If you need spare parts for Torpedo hubs, contact Jens Hansen at torpedo-coasterbrake.com or scheunenfun.de
Anyway, back to the rebuild. All the parts de-greased and cleaned:
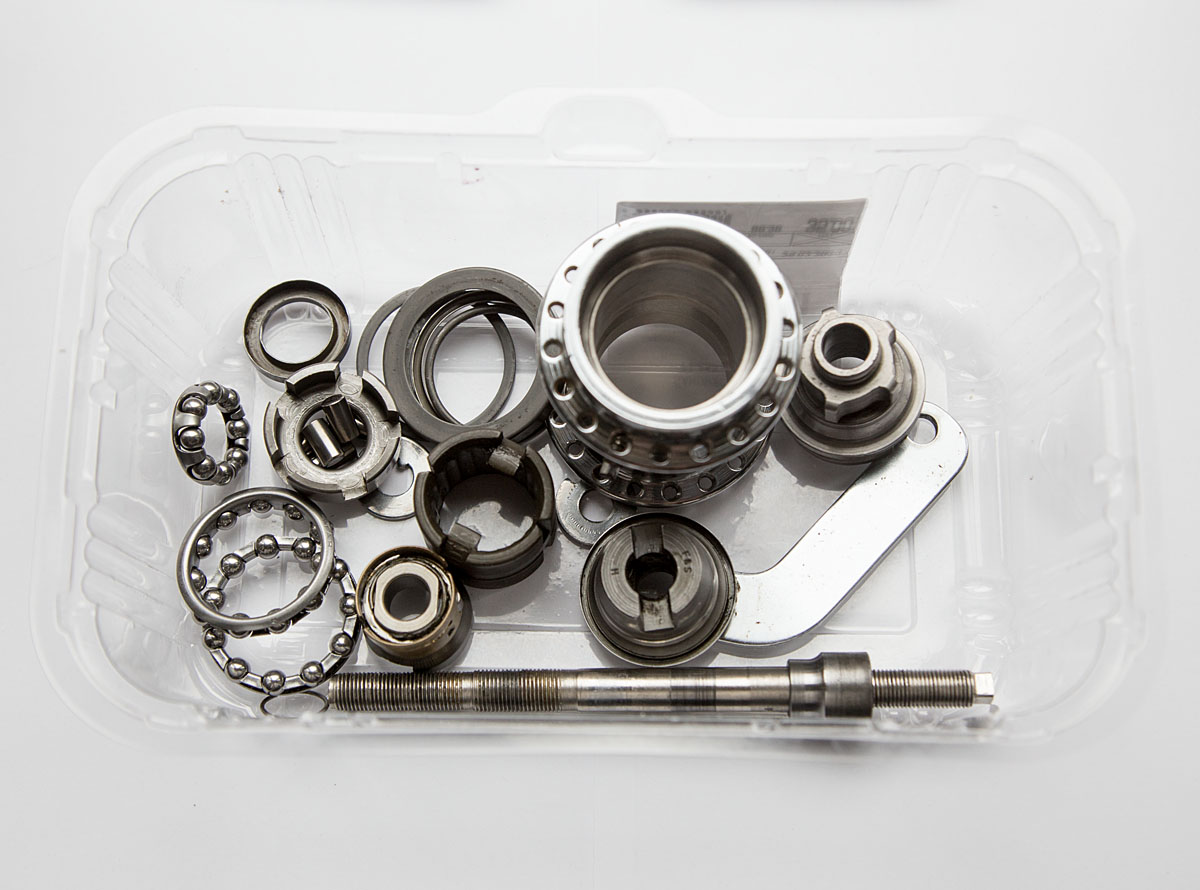
This hub has some minor pitting on the fixed bearing cone on the right side due to some dirt that had entered the bearing. If the pitting is not too deep, the hardened cone can be re-ground in a lathe, or in this case, a poor man's lathe consisting of a electric hand drill mounted in a vise.
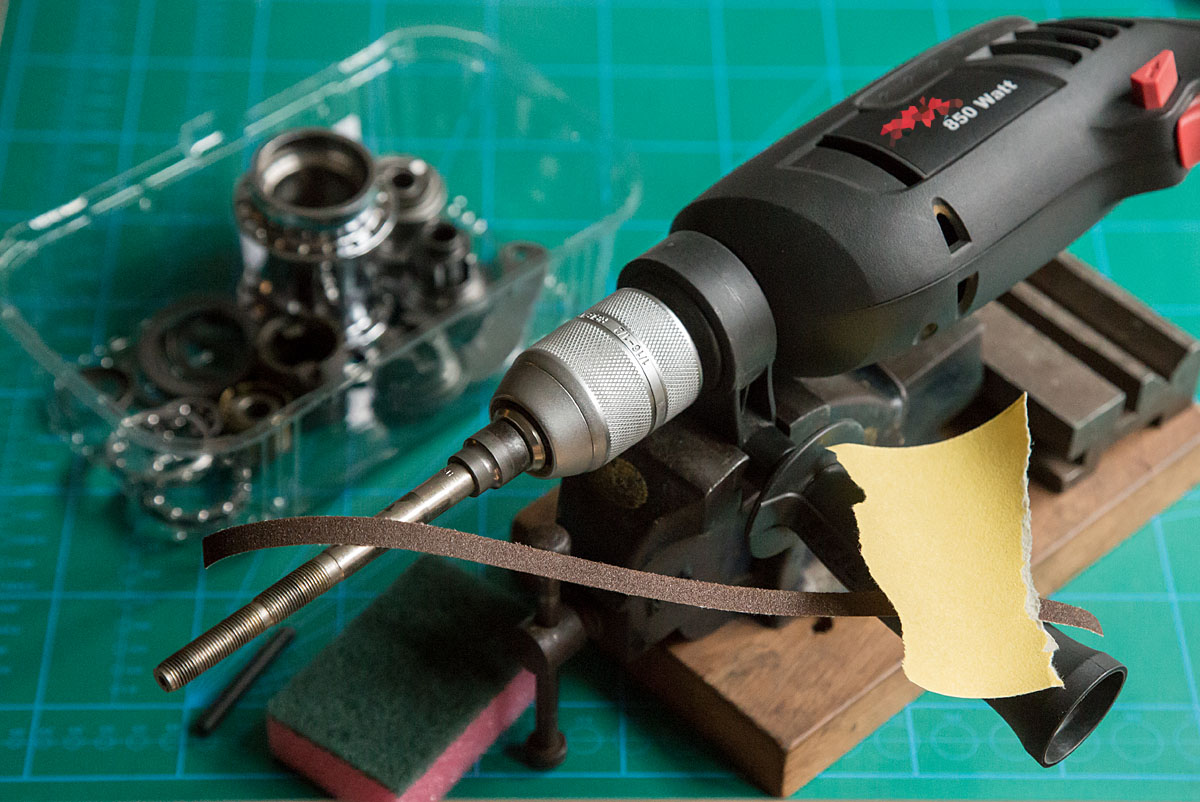
A close-up of the bearing surface damage and a strip of coarse emery cloth (finer grit sand paper and a scrubbing sponge will be used for a finishing polish).
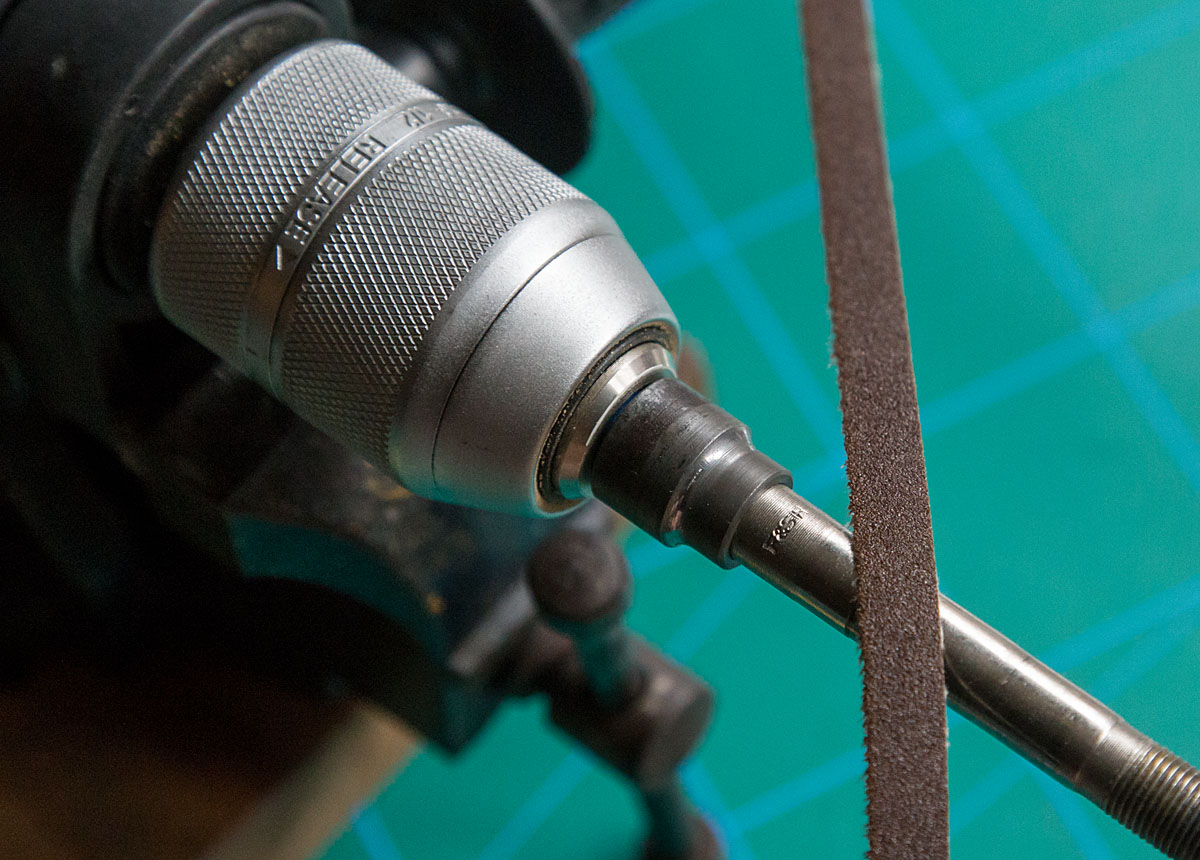
Wrap the emery cloth around a rounded object that matches the contour of the bearing surface and grind the surface, pressing primarily in the axial direction with the drill spinning from half to full speed. Re-position the emery cloth frequently on the rounded object to present a fresh section of cloth, as grinding dust will quickly build up on the emery.
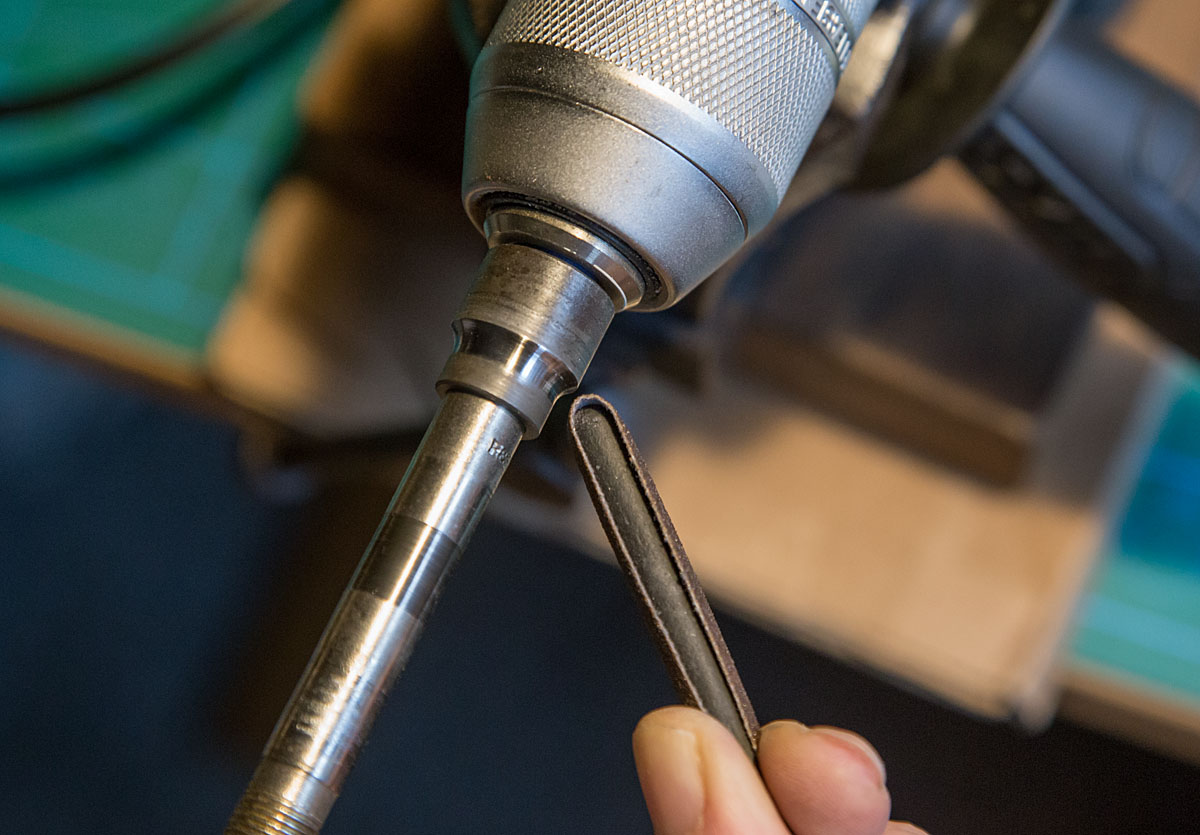
The finished result after polishing with finer grit sand paper and a scrubbing sponge. Painter's tape can also be seen wrapped around the axle, to protect the threads when it was clamped in the drill chuck.
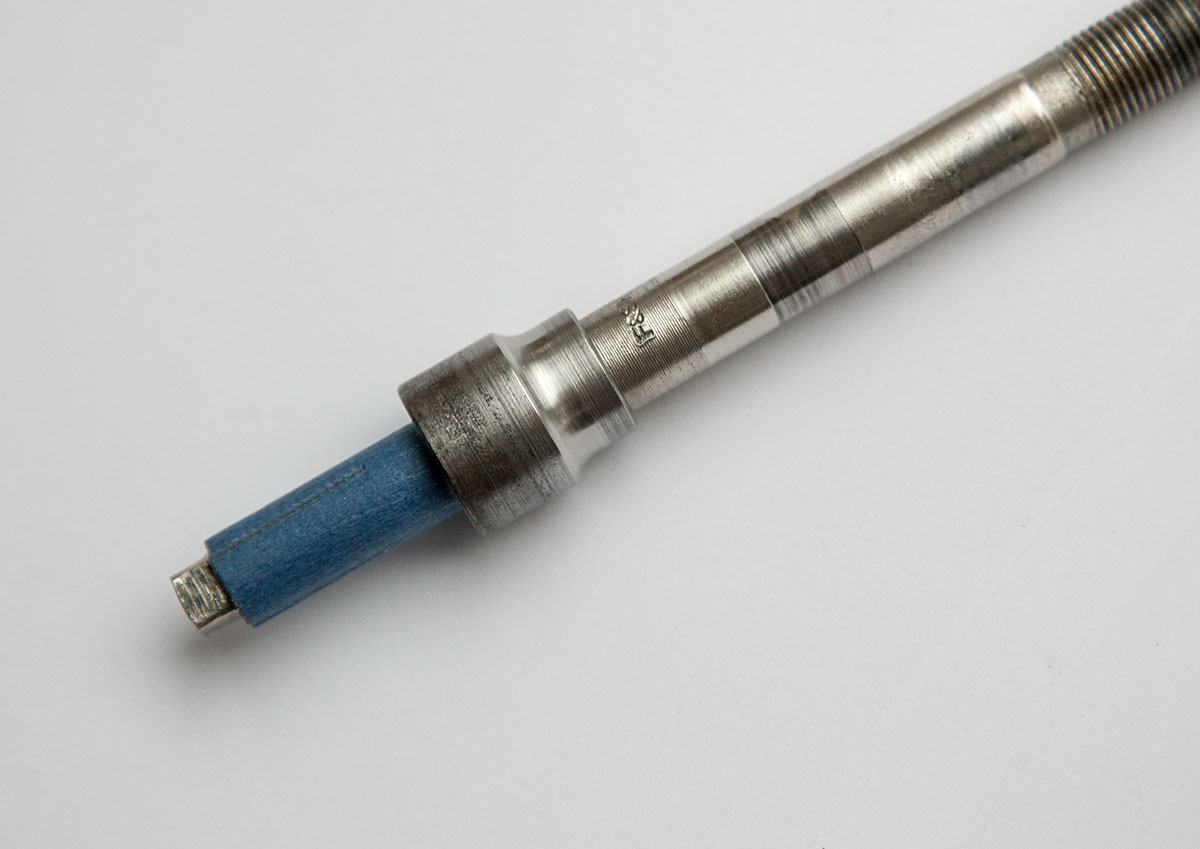
Ready for re-assembly:
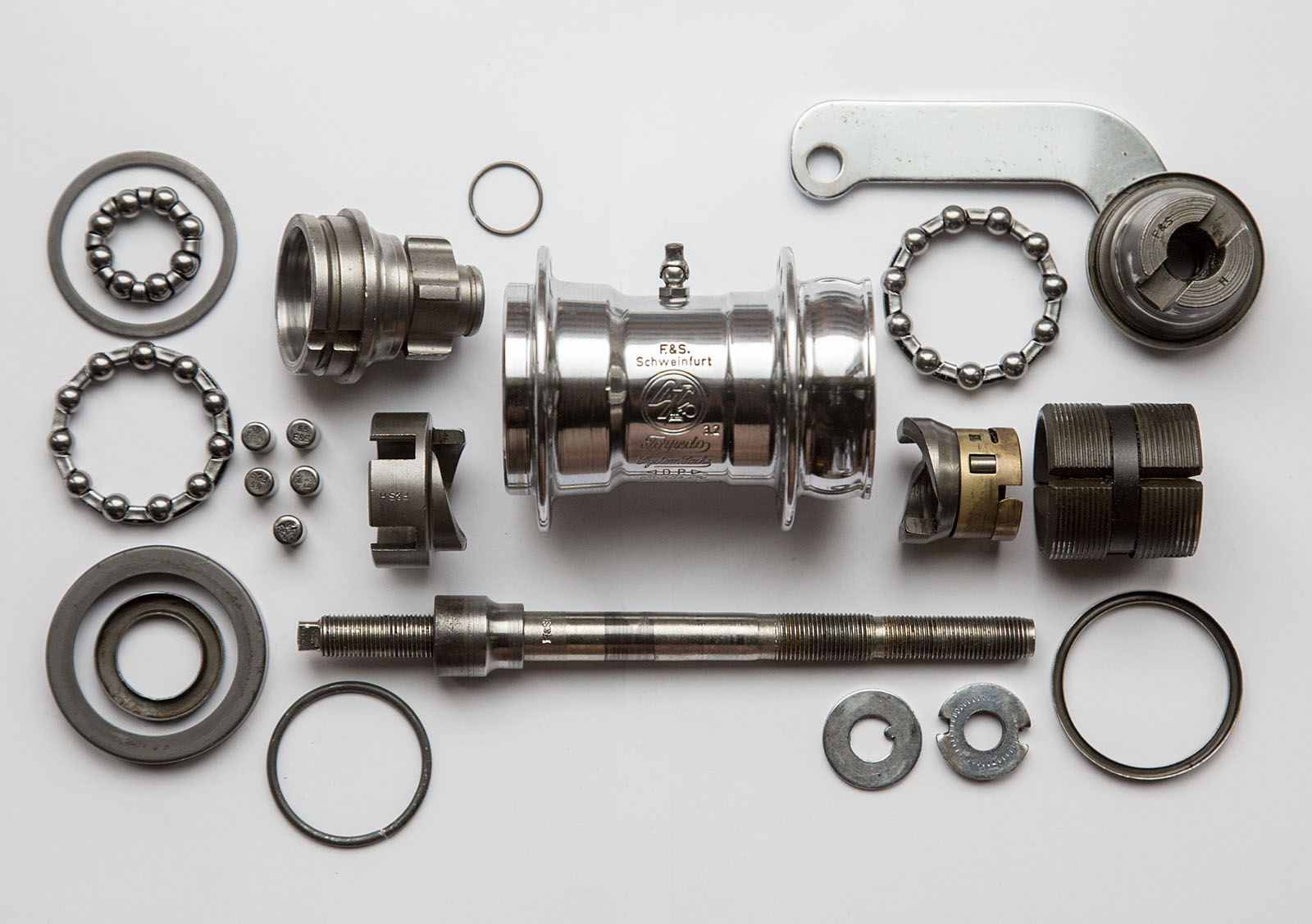
Mount the axle vertically in a vise and build it up starting with the drive side components. The bearings and axle get ball bearing grease, but the freewheel mechanism's ramps, rollers and cage only motor oil. This is very important, as the rollers need to be able to move freely to engage and disengage with the inner hub shell surface.
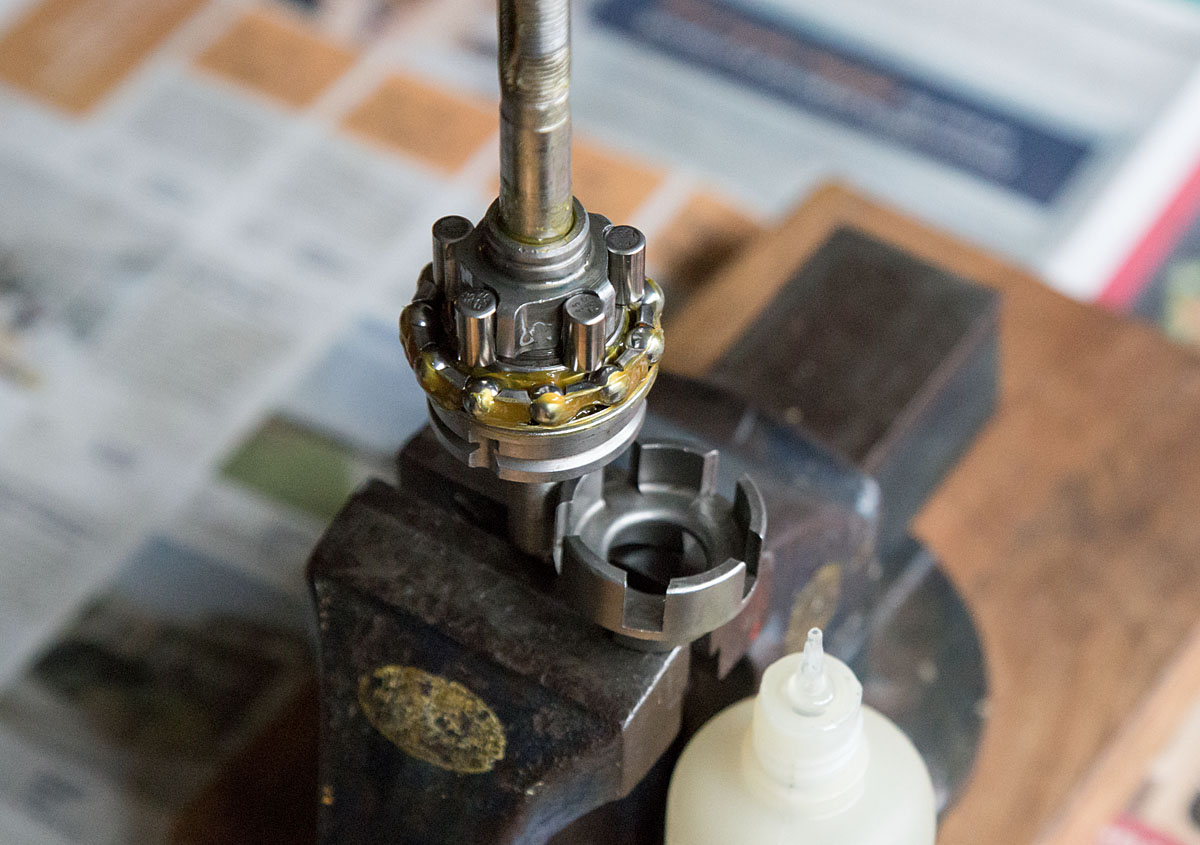
Freewheel mechanism assembly complete.
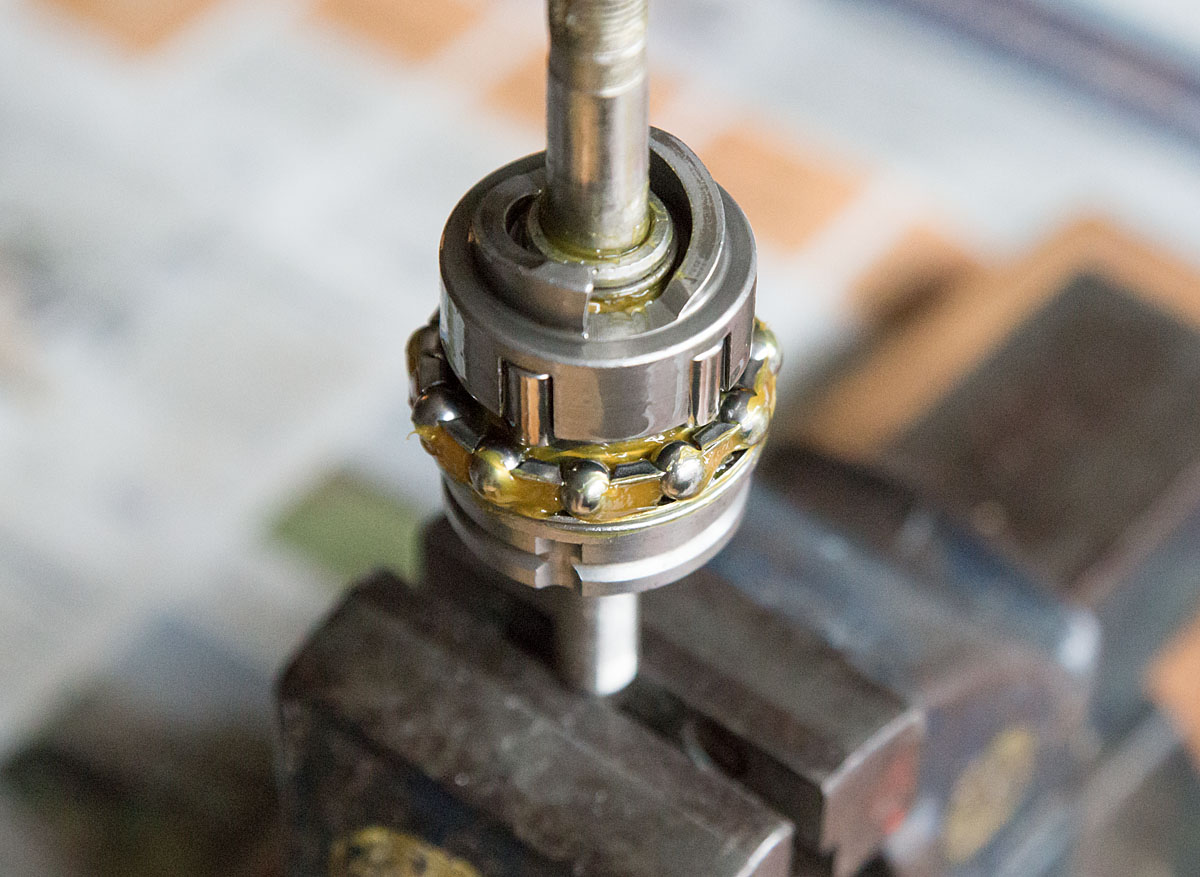
Continue with the build-up and make sure to grease the rest. The brake cylinder must be greased inside and outside with a high temperature resistant brake grease like "Hanseline Bremsmantelfett" (EAN 4002376309455) if it is the later steel version, or with household Vaseline if it is the earlier brass/bronze version (read more about it on scheunenfun.de).
A worn brass brake cylinder will have a shiny, polished surface and poor braking performance. To restore most of the grip, the surface can be cleaned with de-greaser and re-surfaced with sand paper. Make sure to remove as little material as possible, the goal is just to clean it up and expose a fresh surface.
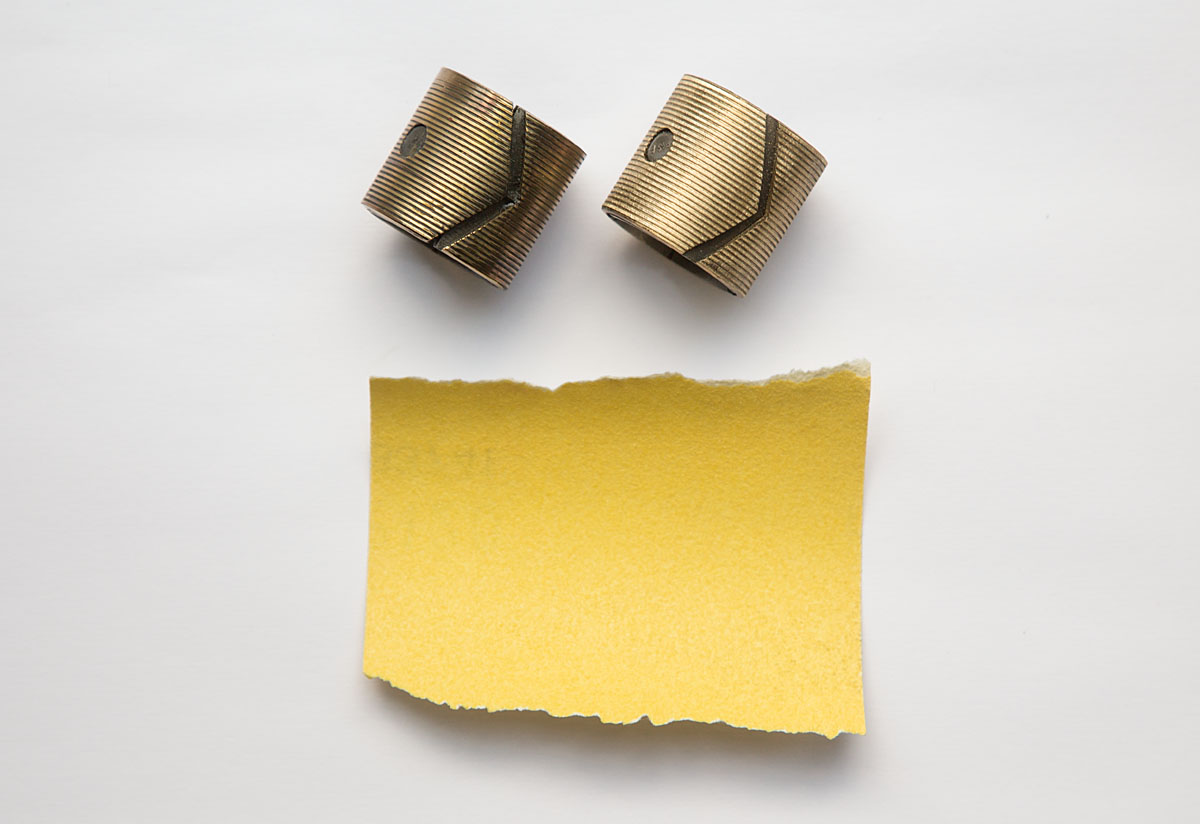
Later in the production the hubs changed to a brake cylinder made of steel which provided more consistent braking performance over its service life. Shown here is the original brass-surface brake cylinder, the replacement steel version introduced in the early '70s, and last a compatible steel cylinder from the "Favorit" clone hub that is still available as a NOS spare part at some online retailers.
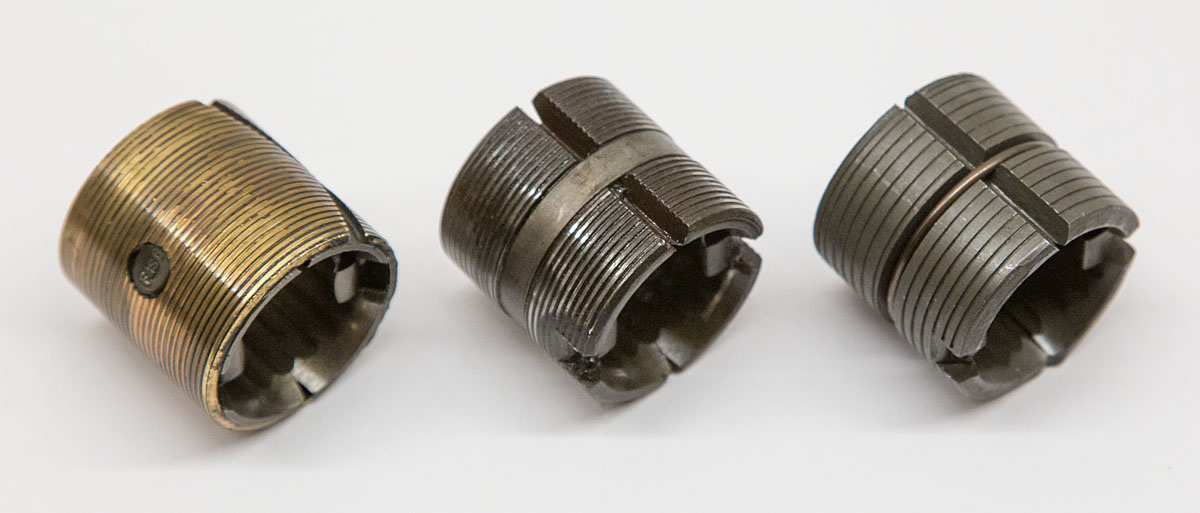
If a fresh clone steel brake cylinder still does not provide enough braking performance, you can experiment with cutting some shallow grooves with an angle grinder with a narrow cutting disc to get a more serrated surface, like this:
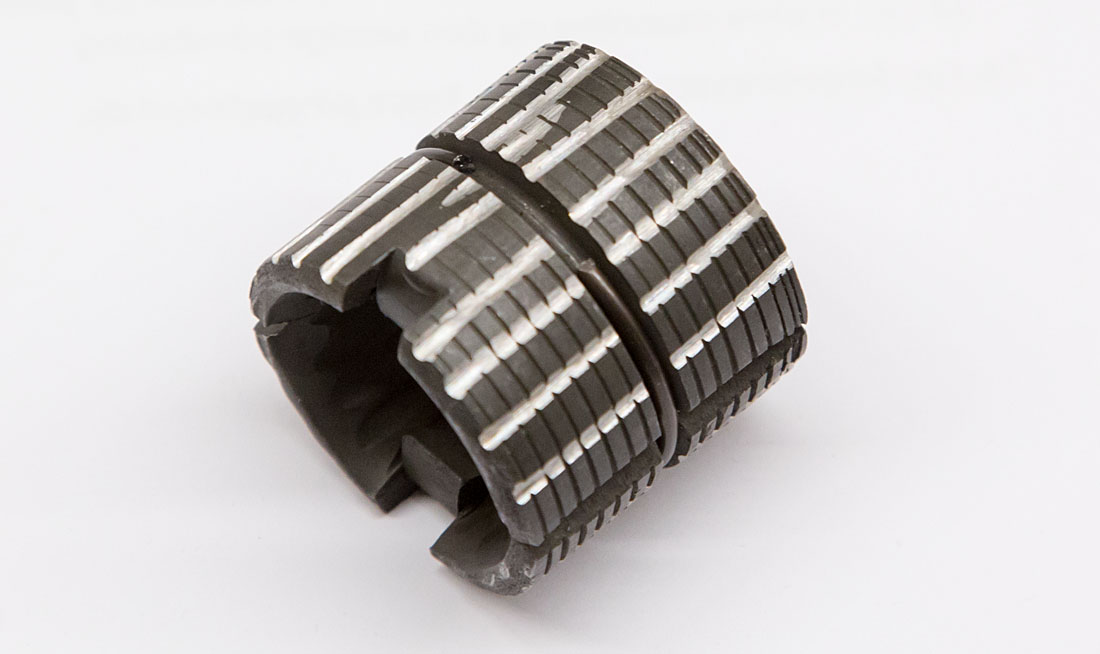
Page last updated 2023-02-25 09:40. Some rights reserved (CC by 3.0)